Ang polycrystalline diamond compact (PDC) at PDC drill bits ay ipinakilala sa merkado sa loob ng ilang dekada. Sa mahabang panahon na ito PDC cutter at PDC drill bit ay nakaranas ng maraming mga pag-urong sa kanilang mga unang yugto, nakaranas din ng mahusay na pag-unlad. Dahan-dahan ngunit sa wakas, unti-unting pinalitan ng mga PDC bit ang mga cone bit ng patuloy na pagpapahusay sa PDC cutter, bit stability, at bit hydraulic structure. Ang mga bit ng PDC ay sumasakop na ngayon ng higit sa 90% ng kabuuang footage ng pagbabarena sa mundo.
Ang PDC Cutter ay unang naimbento ng General Electric (GE) noong 1971. Ang unang PDC Cutter para sa industriya ng langis at gas ay ginawa noong 1973 at sa 3 taon ng experimental at field testing, ito ay ipinakilala sa komersyo noong 1976 matapos itong mapatunayang higit pa mahusay kaysa sa pagdurog ng mga pagkilos ng mga bits ng carbide button.
Sa unang bahagi ng panahon, ang istraktura ng pamutol ng PDC ay ganito: isang carbide round tip, ( diameter 8.38mm, kapal 2.8mm), at isang diamond layer ( kapal 0.5mm na walang chamfer sa ibabaw). Sa oras na iyon, mayroon ding isang Compax "slug system" PDC cutter. Ang istraktura ng cutter na ito ay ganito: ang PDC compax weld sa cemented carbide slug upang mas madaling i-install sa steel body drill bit, at sa gayon ay nagdudulot ng higit na kaginhawahan sa drill bit designer.
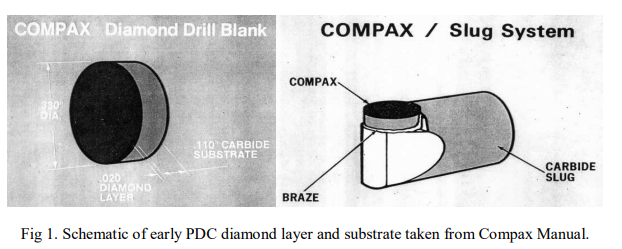
Noong 1973, sinubukan ng GE ang maagang PDC bit nito sa isang balon sa lugar ng King Ranch sa timog Texas. Sa panahon ng pagsubok na proseso ng pagbabarena, ang problema sa paglilinis ng bit ay itinuturing na umiiral. Tatlong ngipin ang nabigo sa brazed joint, at dalawang iba pang ngipin ang nasira kasama ang bahagi ng tungsten carbide. Nang maglaon, sinubukan ng kumpanya ang pangalawang drill bit sa lugar ng Hudson ng Colorado. Pinahusay ng drill bit na ito ang hydraulic structure para sa problema sa paglilinis. Ang bit ay nakamit ang mas mahusay na pagganap sa sandstone-shale formations na may mabilis na bilis ng pagbabarena. Ngunit mayroong ilang mga paglihis mula sa nakaplanong trajectory ng borehole sa panahon ng pagbabarena, at isang maliit na halaga ng pagkawala ng mga PDC cutter ay naganap pa rin dahil sa brazing na koneksyon.
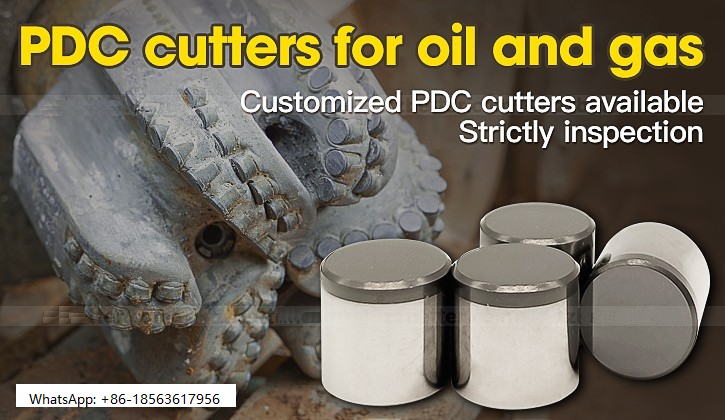
Noong Abril 1974, sinubukan ang ikatlong drill bit sa lugar ng San Juan ng Utah, USA. Ang bit na ito ay napabuti ang istraktura ng ngipin at hugis ng bit. Pinalitan ng bit ang steel body cone bits sa katabing balon, ngunit bumaba ang nozzle at nasira ang bit. Sa oras na iyon, ito ay itinuturing na nangyari malapit sa dulo ng pagbabarena para sa isang matigas na pormasyon, o isang problema na dulot ng pagbagsak ng nozzle.
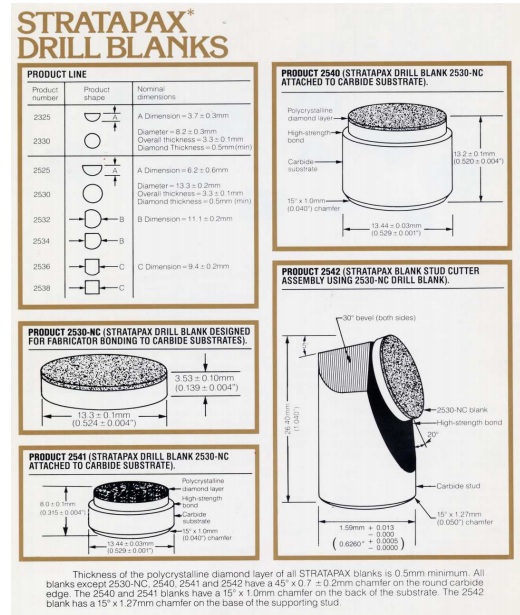
Mula 1974 hanggang 1976, sinuri ng iba't ibang kumpanya ng drill bit at mga negosyante ang iba't ibang pagpapabuti sa PDC cutter. Maraming umiiral na mga problema ang nakatuon sa pananaliksik. Ang nasabing mga resulta ng pananaliksik ay organikong isinama sa mga ngipin ng Stratapax PDC, na inilunsad ng GE noong Disyembre 1976.
Ang pagpapalit ng pangalan mula sa Compax patungong Stratapax ay nakatulong upang maalis ang kalituhan sa industriya ng bit sa pagitan ng mga bit na may tungsten carbide compact, at diamond Compax.
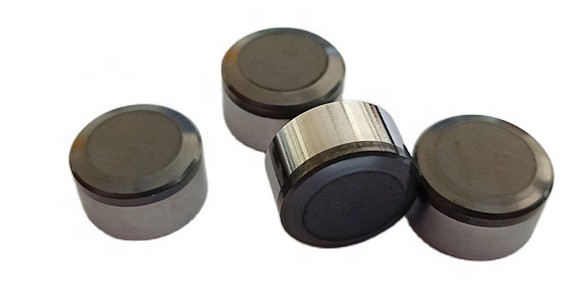
Noong kalagitnaan ng 90s, ang mga tao ay nagsimulang malawakang gumamit ng teknolohiya ng chamfering sa PDC cutting teeth, ang multi-chamfer na teknolohiya ay pinagtibay sa anyo ng isang patent noong 1995. Kung ang teknolohiya ng chamfering ay inilapat nang tama, ang fracture resistance ng PDC cutting teeth maaaring tumaas ng 100%.
Noong 1980s, parehong pinag-aralan ng GE Company (USA) at Sumitomo Company (Japan) ang pag-alis ng kobalt mula sa gumaganang ibabaw ng PDC teeth upang mapabuti ang gumaganang performance ng mga ngipin. Ngunit hindi nila nakamit ang komersyal na tagumpay. Ang isang teknolohiya ay muling binuo at na-patent ng Hycalog(USA). Ito ay pinatunayan na kung ang metal na materyal ay maaaring alisin mula sa butil gap, ang thermal katatagan ng PDC teeth ay lubos na mapabuti upang ang bit ay maaaring mag-drill ng mas mahusay sa mas mahirap at mas abrasive formations. Pinapabuti ng teknolohiyang ito sa pagtanggal ng cobalt ang wear resistance ng PDC teeth sa mga napaka-abrasive na hard rock formation at higit na pinalalawak ang application range ng PDC bits.
Simula noong 2000, ang aplikasyon ng PDC bits ay mabilis na lumawak. Ang mga pormasyon na hindi ma-drill gamit ang PDC bits ay unti-unting nagagawang ma-drill nang matipid at mapagkakatiwalaan gamit ang PDC drill bits.
Noong 2004, sa industriya ng drill bit, ang kita sa merkado ng mga drill bit ng PDC ay sumasakop ng halos 50%, at ang distansya ng pagbabarena ay umabot sa halos 60%. Ang paglago na ito ay nagpapatuloy hanggang ngayon. Halos lahat ng kasalukuyang ginagamit sa North American drilling application ay PDC bits.
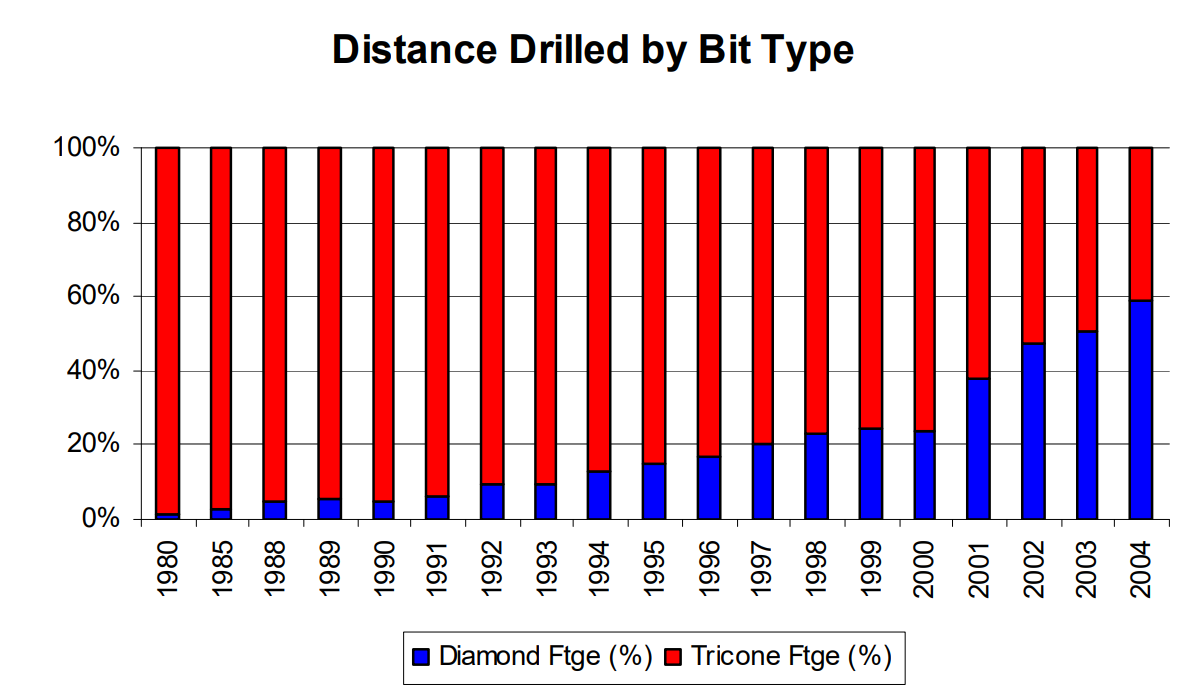
Sa madaling salita, mula nang ilunsad ito noong dekada 70 at naranasan ang paunang mabagal na paglaki nito, unti-unting itinaguyod ng mga PDC cutter ang patuloy na pag-unlad ng industriya ng drill bit para sa paggalugad at pagbabarena ng langis at gas. Malaki ang epekto ng teknolohiya ng PDC sa industriya ng pagbabarena.
Ang mga bagong pasok sa merkado ng mga de-kalidad na PDC cutting teeth, pati na rin ang mga pangunahing kumpanya ng drill, ay patuloy na namumuno sa reporma at inobasyon ng mga Innovative na materyales at proseso ng produksyon upang ang performance ng PDC cutting teeth at PDC drill bits ay patuloy na mapabuti.
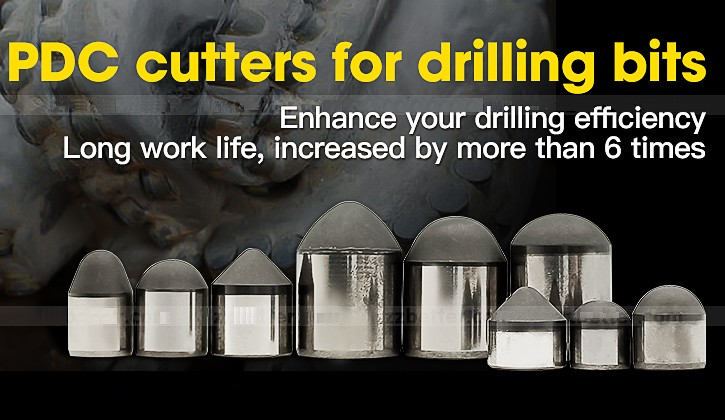

Oras ng post: Abr-07-2023